脱硫脱硝深度除尘一体塔技术/Desulfurization, Denitration and Deep Dedusting Integrated Tower
脱硫、脱硝深度除尘一体塔 新工艺介绍
Technique Features of Desulfurization, Denitration and Deep Dedusting Integrated Tower
◆ 高新技术 Advanced technology, International initiative
◆ 低排放 Ultra-low emissions
◆ 水系统全部闭式循环,无二次污染 Totally enclosed water circulation system, no secondary pollution
◆ 设备占地面积小 Equipment covers a small area
◆ 设备造价及运营成本比传统工艺低 Equipment cost and operating cost lower than those of the traditional
◆ 可以燃烧高硫煤
特有技术:脱硫脱硝深度除尘一体塔技术介绍
Technique Features and Performance Parameters of Desulfurization, Denitration and Deep Dedusting Integrated Tower
(一)新技术的特点及优势 / Features and advantages of the new technology
1、脱氮效率高
对烟气温度无特殊要求,脱氮效率高达85-95%由于采用了先进的氧化还原技术且与脱硫同步完成。故此运行费用低,这是目前“SCR”和“SNCR”不能达到的。脱硫脱硝用水全部闭路循环,且配置了中水脱氯装置不向外排废水,无二次污染。在烟气脱硫脱硝塔内,利用多道逆顺向喷淋法,将吸收液喷入烟气中,在高速气流的带动下,吸收液被吹成雾状,比表面积大,使气液接触更加充分。从而确保了脱硫脱硝效率的稳定。
2、脱硫脱硝除尘一体化
由于氧化还原后的循环液活性好,故此对SO2的吸收速度快且效率高。根据试验结果表明脱硫效率高达99.1%,石灰-石膏法及石灰石-石膏法所不能达到的。由于塔体上部安装了水洗除尘装置。故此大大提高了塔体的除尘效率。一般湿式空塔喷雾技术除尘效率一般在60-80%湿式静电也不超过90%,而我们的湿式水洗除尘技术除尘技术高达98.5%也将脱硫后的颗粒物的排放浓度降到10mg/Nm3以下,达到超低排放标准。
3、投资少、故障率低
在目前应用的湿式静电除尘技术中,投资大。且运行费用高、电耗大。且存在着运行不稳定的问题。而我们湿式除尘技术由于循环的是清水,且闭路循环,故此故障率低,效果稳定。系统可保证长期正常稳定运行,且维护量非常小。脱硫脱硝塔不含易造成结垢的部件,且采用氨碱液作为吸收液,有效避免了喷嘴的堵塞,不存在结垢和堵塞等问题。设备检修不影响系统的正常运转,系统正常运转率98%以上。运行费用低。在传统脱硫脱硝运行费用中脱硫脱硝剂费用占较大比例,而本系统使用硫酸铵做氨源且循环使用,理论上不消耗,实际循环的是石灰和极少量的氨以及催化剂,所以运行费用较低。
1. High denitrification efficiency
There is no special requirement for temperature of the flue gas, and the denitrification efficiency is up to 85 to 95% due to the adoption of advanced oxidation reduction technology and the synchronous completion of desulfurization. Therefore, the operating cost is low, which cannot be attained by "SCR" and "SNCR" currently. The used water of desulfurization and denitration applies closed cycle, and reclaimed water dechlorinating device has been deployed in order to avoid the discharge of waste water, without secondary pollution. In the desulfurization& denitration tower for flue gas, by multi-channel inverse&forward spray method, the absorption liquid has be injected into the flue gas. Under the drive of high speed airflow, the absorption liquid was blown into the mist shape with a larger specific surface area, allowing the gas-liquid contact more adequate, so as to ensure the stability of desulfurization and denitration efficiency.
2. Integration of desulfurization, denitration and dedusting
Due to the good activity of the recycled liquid undergoing oxidation and reduction, its absorption rate of SO2 is fast and efficient. According to the experimental results, the desulfurization efficiency reached 99.1%, which cannot be obtained by the lime - gypsum method and the limestone -gypsum method. Because the top tower body is equipped with a water washing dedusting device, the dedusting efficiency of the tower body has been greatly improved. In general, the dedusting efficiency of wet void tower spray technology is 60 to 80%, and the efficiency of wet static electricity is no more than 90%, while the efficiency of our wet water washing dedusting technology is up to 98.5%, meanwhile the emission concentration of particulate matter after desulfurization dropped to below 10mg/Nm3, reaching the ultra low emission standard.
3. Low investment, low failure rate
The currently applied wet electrostatic dedusting technology requires large investment, high operation cost and large power onsumption, as well as the problem of unstable operation. The circulated water in our wet dedusting technology is clean water, and losed cycle is applied, so the failure rate is low, the effect is stable. The system can guarantee long-term normal and stable operation, with ew maintenance quantity. Desulfurization& denitration tower does not contain components easy to cause scale formation and employs mmonia alkali solution as the absorption liquid, effectively avoiding the nozzle clogging and problems of scale formation and plugging. quipment maintenance does not affect the normal running of the system, and the system normal running rate reaches 98% or more, requiring low operating cost. Absorbent of desulfurization and denitrification accounted for a higher proportion in the traditional esulfurization& denitration operating cost, and the system uses ammonium sulfate as resource of ammonia, which has been recycled. The mmonium sulfate is not consumed in theory, while the matters in actual circulation are lime, tiny ammonia and catalysts, so the perating cost is lower.
(二)工艺流程及工作原理 / Process flow and working principle
1. 工艺流程图 Process flow diagram
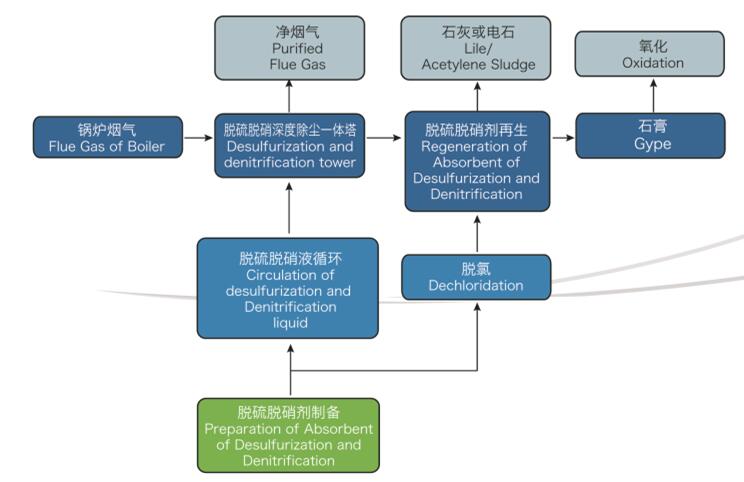
2. 设备连接 Device connection
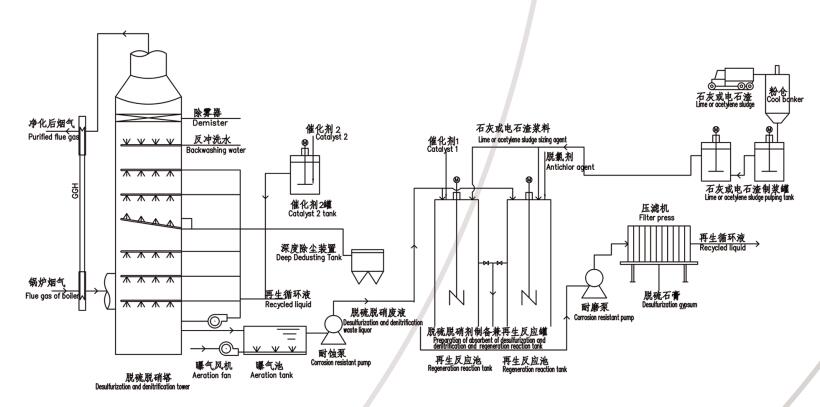
3. 脱硫脱硝反应原理 Principle of desulfurization and denitrification reaction
本方案采用循环氨碱法吸收烟气中的SO2和NOx,即用氨碱液作为脱硫脱硝剂,石灰作为氨碱循环再生剂。其基本原理是:氨进入脱硫塔内吸收烟气中的二氧化硫、氮氧化物,再用石灰浆(主要成份为Ca(OH)2)将脱硫脱硝产物再生置换出氨重新返回到脱硫脱硝塔内脱硫脱硝。
The scheme adopts cycling ammonia-alkali method to absorb SO2 and NOx in flue gas, namely using ammonia alkali liquor as the absorbent of desulfurization and denitrification, and lime as ammonia alkali recycling agent. The basic principle is as follows: inject ammonia into the desulfurization tower to absorb sulfur dioxide and nitrogen oxides in the flue gas, and then use lime slurry (the main ingredient is Ca(OH)2) to regenerate the desulfurization and denitrification products for replacement of ammonia, finally the ammonia is returned to desulfurization& denitrification tower for desulfurization and denitrification.
主要反应机理如下:
The main reaction mechanism is as follows:
(1)二氧化硫、氮氧化物的吸收反应 Absorption reaction of SO2 and NOx
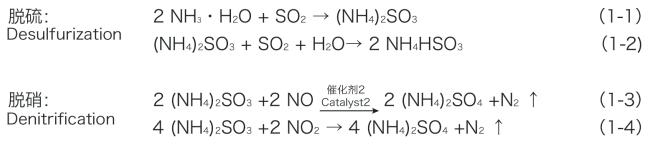
(2)氨碱液再生反应 Ammonia alkali regeneration reaction

(3)氨碱液再生反应 Intra-system side reaction

其中,催化剂1、催化剂2的作用是为了大幅度提高反应(1-3)、(2-1)、(2-2)的反应速度。
In the above, the function of catalyst 1 or catalyst 2 is to largely increase the reaction rate of (1-3), (2-1) and (2-2).
(三)设计原则 / Design principles
(1)脱硫脱硝工艺遵循技术成熟、设备先进运行稳定、操作维护方便、自动化程度较高、运行成本较低、无二次污染原则。能够保证高可用率、高脱硫脱硝率、低石灰消耗量、低压用电量及低耗水量,而且完全符合环境保护要求。
(2)脱硫脱硝系统从锅炉炉型、负荷、炉后脱硫脱硝场地等诸多方面因素考虑,提出合理的脱硫脱硝工艺方案。
(3)脱硫脱硝工艺充分考虑锅炉特点,系统阻力稳定,脱硫脱硝装置在启、停、运行及事故处理情况下不影响锅炉正常运行。
(4)脱硫脱硝工艺适应锅炉风量、温度、SO2、NOx浓度等负荷变化与波动。
(5)脱硫脱硝工艺与设备布置合理,能满足业主方提的总图位置要求。文中所叙述的系统和布置是基本要求,通过详细的工艺设计、实现所有的工程要求,建造一个完整的脱硫脱硝装置。
(6)脱硫脱硝剂和副产物物料输送、循环流畅,能力匹配。
(7)脱硫脱硝主体设备设计使用寿命不低于15年。
(8)脱硫脱硝剂价格比较低廉、易于获得。
(9)脱硫脱硝装置采用DCS控制,同时考虑与主体工程的信号连接,预留通讯接口。
(10)脱硫脱硝副产物石膏含水率小于10%,用汽车外运,综合利用。
(11)脱硫脱硝后烟气汇总后进烟囱(需防腐,需方负责)排放。
(12)整个烟气脱硫脱硝系统的所有建(构)筑物布置与主体工程协调。并根据其工程设计的要和布置要求在所给定的区域范围内优化,以使其工艺流程和布置合理、安全和经济。
(13)脱硫脱硝区域水、电、气使用,将在与主厂总管连接的分管道上安装计量装置,并将这些能源计量数据纳入控制系统显示,并预留与主装置CEMS系统对接的信息接口。
(14)供方提出烟气脱硫脱硝系统所需工业水(工艺水、各转动设备的冷却水)的水质、水压、水量要求,以及仪用压缩空气用量和相关参数要求。需方将负责提烟气脱硫脱硝系统所用的工业水源。烟气脱硫脱硝系统所的压缩空气气源由需方负责。烟气脱硫脱硝系统在移交之前所的施工和调试用的工业水、蒸汽等将由需方提接口位置。要求,以及仪用压缩空气用量和相关参数要求。需方将负责提烟气脱硫脱硝系统所用的工业水源。烟气脱硫脱硝系统所的压缩空气气源由需方负责。烟气脱硫脱硝系统在移交之前所的施工和调试用的工业水、蒸汽等将由需方提接口位置。
(1) The desulfurization and denitrification process follows the principle of mature technology, advanced equipment, stable running, convenient operation and maintenance, high degree of automation, low operating costs and none secondary pollution. High availability, high desulfurization and denitrification rate, low lime consumption, low power consumption and low water consumption are ensured, and the standard of environmental protection is fully met.
(2) The desulfurization and denitrification system takes the boiler type, load, furnace rear desulfurization and denitrification sites, and many other factors into consideration, putting forward a reasonable desulfurization and denitrification process program.
(3) The desulfurization and denitrification process fully considers the characteristics of the boiler. The system resistance is stable. The desulfurization and denitrification device doesn’t affect the normal operating of the boiler in the start, stop, operating and accident handling conditions.
(4) The desulfurization and denitrification process adapts to air quantity, temperature, concentration of SO2 or NOx and other load changes and fluctuations of the boiler.
(5) The deploy of desulfurization & denitrification processes and devices is reasonable, meeting the requirements of placement of eneral layout proposed by the owner. The system and layout described in this paper are the basic requirements by detailed process design, all the engineering demands are achieved to construct a complete desulfurization and denitrification device.
(6) Material conveying and circulation of absorbent of desulfurization and denitrification and the by-products are smooth, with capability matching.
(7) The service life of the main equipment for desulfurization and denitrification is designed to be no less than 15 years.
(8) The absorbent of desulfurization and denitrification is relatively inexpensive and easy to be obtained.
(9) The desulfurization and denitrification device adopts DCS control, and takes the signal connection with the main project into consideration, reserving communication interface.
(10) Water content of desulfurization and denitrification by-product gypsum is less than 10%, and automobile is used for outward transport and comprehensive utilization of the by-product.
(11) The flue gas after desulfurization and denitrification is collected for discharge through chimney (anticorrosion is required and the demander is in charge).
(12) The deploy of all the buildings (structures) in the entire flue gas desulfurization and denitrification system should coordinate with the main project. The deploy should be optimized in the given area according to its engineering design and deploy requirements, so that the process flow and deploy are reasonable, safe and economic.
(13) For the use of water, electricity and gas in the area of desulfurization and denitrification, metering mechanism will be installed on the sub pipeline connected to the total pipeline of the main plant, and the energy metering data is incorporated in the control system for display, reserving the information interface jointing the CEMS system of the main device.
(14)The supplier puts forward requirements on water quality, water pressure and water volume of the industrial water (process water, cooling water of the rotating equipment) required by the flue gas desulfurization and denitrification system, as well as the requirements on the consumption of compressed air for instrument and related parameters. The demander will be responsible for the industrial water source used in the flue gas desulfurization and denitrification system. The demander is also responsible for the compressed air source used by the flue gas desulfurization and denitrification system. Before handing over of the flue gas desulfurization and denitrification system, the industrial water and steam used in construction and commissioning will be provided by the demander.
the industrial water (process water, cooling water of the rotating equipment) required by the flue gas desulfurization and denitrification system, as well as the requirements on the consumption of compressed air for instrument and related parameters. The demander will be responsible for the industrial water source used in the flue gas desulfurization and denitrification system. The demander is also responsible for the compressed air source used by the flue gas desulfurization and denitrification system. Before handing over of the flue gas desulfurization and denitrification system, the industrial water and steam used in construction and commissioning will be provided by the demander.
(四)性能参数及运行分析 / Performance parameters and operation analysis
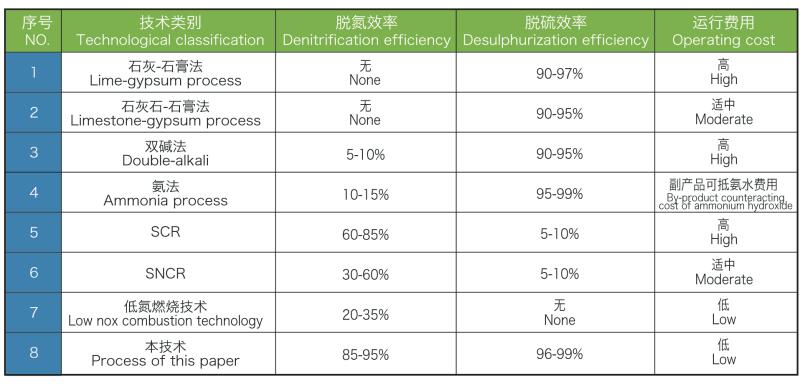
Technique Features of Desulfurization, Denitration and Deep Dedusting Integrated Tower
◆ 高新技术 Advanced technology, International initiative
◆ 低排放 Ultra-low emissions
◆ 水系统全部闭式循环,无二次污染 Totally enclosed water circulation system, no secondary pollution
◆ 设备占地面积小 Equipment covers a small area
◆ 设备造价及运营成本比传统工艺低 Equipment cost and operating cost lower than those of the traditional
◆ 可以燃烧高硫煤
特有技术:脱硫脱硝深度除尘一体塔技术介绍
Technique Features and Performance Parameters of Desulfurization, Denitration and Deep Dedusting Integrated Tower
(一)新技术的特点及优势 / Features and advantages of the new technology
1、脱氮效率高
对烟气温度无特殊要求,脱氮效率高达85-95%由于采用了先进的氧化还原技术且与脱硫同步完成。故此运行费用低,这是目前“SCR”和“SNCR”不能达到的。脱硫脱硝用水全部闭路循环,且配置了中水脱氯装置不向外排废水,无二次污染。在烟气脱硫脱硝塔内,利用多道逆顺向喷淋法,将吸收液喷入烟气中,在高速气流的带动下,吸收液被吹成雾状,比表面积大,使气液接触更加充分。从而确保了脱硫脱硝效率的稳定。
2、脱硫脱硝除尘一体化
由于氧化还原后的循环液活性好,故此对SO2的吸收速度快且效率高。根据试验结果表明脱硫效率高达99.1%,石灰-石膏法及石灰石-石膏法所不能达到的。由于塔体上部安装了水洗除尘装置。故此大大提高了塔体的除尘效率。一般湿式空塔喷雾技术除尘效率一般在60-80%湿式静电也不超过90%,而我们的湿式水洗除尘技术除尘技术高达98.5%也将脱硫后的颗粒物的排放浓度降到10mg/Nm3以下,达到超低排放标准。
3、投资少、故障率低
在目前应用的湿式静电除尘技术中,投资大。且运行费用高、电耗大。且存在着运行不稳定的问题。而我们湿式除尘技术由于循环的是清水,且闭路循环,故此故障率低,效果稳定。系统可保证长期正常稳定运行,且维护量非常小。脱硫脱硝塔不含易造成结垢的部件,且采用氨碱液作为吸收液,有效避免了喷嘴的堵塞,不存在结垢和堵塞等问题。设备检修不影响系统的正常运转,系统正常运转率98%以上。运行费用低。在传统脱硫脱硝运行费用中脱硫脱硝剂费用占较大比例,而本系统使用硫酸铵做氨源且循环使用,理论上不消耗,实际循环的是石灰和极少量的氨以及催化剂,所以运行费用较低。
1. High denitrification efficiency
There is no special requirement for temperature of the flue gas, and the denitrification efficiency is up to 85 to 95% due to the adoption of advanced oxidation reduction technology and the synchronous completion of desulfurization. Therefore, the operating cost is low, which cannot be attained by "SCR" and "SNCR" currently. The used water of desulfurization and denitration applies closed cycle, and reclaimed water dechlorinating device has been deployed in order to avoid the discharge of waste water, without secondary pollution. In the desulfurization& denitration tower for flue gas, by multi-channel inverse&forward spray method, the absorption liquid has be injected into the flue gas. Under the drive of high speed airflow, the absorption liquid was blown into the mist shape with a larger specific surface area, allowing the gas-liquid contact more adequate, so as to ensure the stability of desulfurization and denitration efficiency.
2. Integration of desulfurization, denitration and dedusting
Due to the good activity of the recycled liquid undergoing oxidation and reduction, its absorption rate of SO2 is fast and efficient. According to the experimental results, the desulfurization efficiency reached 99.1%, which cannot be obtained by the lime - gypsum method and the limestone -gypsum method. Because the top tower body is equipped with a water washing dedusting device, the dedusting efficiency of the tower body has been greatly improved. In general, the dedusting efficiency of wet void tower spray technology is 60 to 80%, and the efficiency of wet static electricity is no more than 90%, while the efficiency of our wet water washing dedusting technology is up to 98.5%, meanwhile the emission concentration of particulate matter after desulfurization dropped to below 10mg/Nm3, reaching the ultra low emission standard.
3. Low investment, low failure rate
The currently applied wet electrostatic dedusting technology requires large investment, high operation cost and large power onsumption, as well as the problem of unstable operation. The circulated water in our wet dedusting technology is clean water, and losed cycle is applied, so the failure rate is low, the effect is stable. The system can guarantee long-term normal and stable operation, with ew maintenance quantity. Desulfurization& denitration tower does not contain components easy to cause scale formation and employs mmonia alkali solution as the absorption liquid, effectively avoiding the nozzle clogging and problems of scale formation and plugging. quipment maintenance does not affect the normal running of the system, and the system normal running rate reaches 98% or more, requiring low operating cost. Absorbent of desulfurization and denitrification accounted for a higher proportion in the traditional esulfurization& denitration operating cost, and the system uses ammonium sulfate as resource of ammonia, which has been recycled. The mmonium sulfate is not consumed in theory, while the matters in actual circulation are lime, tiny ammonia and catalysts, so the perating cost is lower.
(二)工艺流程及工作原理 / Process flow and working principle
1. 工艺流程图 Process flow diagram
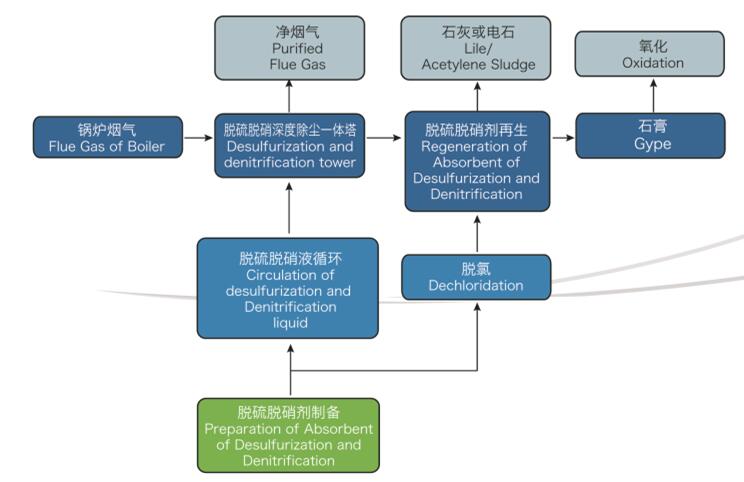
2. 设备连接 Device connection
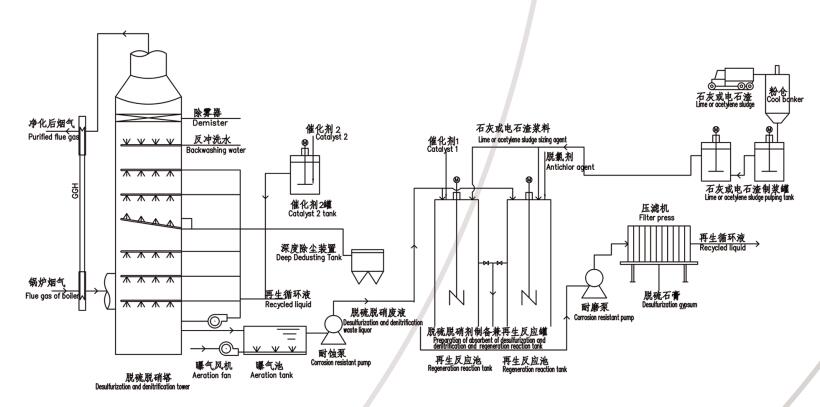
3. 脱硫脱硝反应原理 Principle of desulfurization and denitrification reaction
本方案采用循环氨碱法吸收烟气中的SO2和NOx,即用氨碱液作为脱硫脱硝剂,石灰作为氨碱循环再生剂。其基本原理是:氨进入脱硫塔内吸收烟气中的二氧化硫、氮氧化物,再用石灰浆(主要成份为Ca(OH)2)将脱硫脱硝产物再生置换出氨重新返回到脱硫脱硝塔内脱硫脱硝。
The scheme adopts cycling ammonia-alkali method to absorb SO2 and NOx in flue gas, namely using ammonia alkali liquor as the absorbent of desulfurization and denitrification, and lime as ammonia alkali recycling agent. The basic principle is as follows: inject ammonia into the desulfurization tower to absorb sulfur dioxide and nitrogen oxides in the flue gas, and then use lime slurry (the main ingredient is Ca(OH)2) to regenerate the desulfurization and denitrification products for replacement of ammonia, finally the ammonia is returned to desulfurization& denitrification tower for desulfurization and denitrification.
主要反应机理如下:
The main reaction mechanism is as follows:
(1)二氧化硫、氮氧化物的吸收反应 Absorption reaction of SO2 and NOx
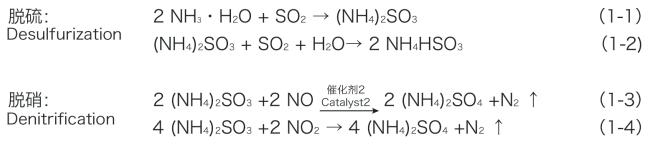
(2)氨碱液再生反应 Ammonia alkali regeneration reaction

(3)氨碱液再生反应 Intra-system side reaction

其中,催化剂1、催化剂2的作用是为了大幅度提高反应(1-3)、(2-1)、(2-2)的反应速度。
In the above, the function of catalyst 1 or catalyst 2 is to largely increase the reaction rate of (1-3), (2-1) and (2-2).
(三)设计原则 / Design principles
(1)脱硫脱硝工艺遵循技术成熟、设备先进运行稳定、操作维护方便、自动化程度较高、运行成本较低、无二次污染原则。能够保证高可用率、高脱硫脱硝率、低石灰消耗量、低压用电量及低耗水量,而且完全符合环境保护要求。
(2)脱硫脱硝系统从锅炉炉型、负荷、炉后脱硫脱硝场地等诸多方面因素考虑,提出合理的脱硫脱硝工艺方案。
(3)脱硫脱硝工艺充分考虑锅炉特点,系统阻力稳定,脱硫脱硝装置在启、停、运行及事故处理情况下不影响锅炉正常运行。
(4)脱硫脱硝工艺适应锅炉风量、温度、SO2、NOx浓度等负荷变化与波动。
(5)脱硫脱硝工艺与设备布置合理,能满足业主方提的总图位置要求。文中所叙述的系统和布置是基本要求,通过详细的工艺设计、实现所有的工程要求,建造一个完整的脱硫脱硝装置。
(6)脱硫脱硝剂和副产物物料输送、循环流畅,能力匹配。
(7)脱硫脱硝主体设备设计使用寿命不低于15年。
(8)脱硫脱硝剂价格比较低廉、易于获得。
(9)脱硫脱硝装置采用DCS控制,同时考虑与主体工程的信号连接,预留通讯接口。
(10)脱硫脱硝副产物石膏含水率小于10%,用汽车外运,综合利用。
(11)脱硫脱硝后烟气汇总后进烟囱(需防腐,需方负责)排放。
(12)整个烟气脱硫脱硝系统的所有建(构)筑物布置与主体工程协调。并根据其工程设计的要和布置要求在所给定的区域范围内优化,以使其工艺流程和布置合理、安全和经济。
(13)脱硫脱硝区域水、电、气使用,将在与主厂总管连接的分管道上安装计量装置,并将这些能源计量数据纳入控制系统显示,并预留与主装置CEMS系统对接的信息接口。
(14)供方提出烟气脱硫脱硝系统所需工业水(工艺水、各转动设备的冷却水)的水质、水压、水量要求,以及仪用压缩空气用量和相关参数要求。需方将负责提烟气脱硫脱硝系统所用的工业水源。烟气脱硫脱硝系统所的压缩空气气源由需方负责。烟气脱硫脱硝系统在移交之前所的施工和调试用的工业水、蒸汽等将由需方提接口位置。要求,以及仪用压缩空气用量和相关参数要求。需方将负责提烟气脱硫脱硝系统所用的工业水源。烟气脱硫脱硝系统所的压缩空气气源由需方负责。烟气脱硫脱硝系统在移交之前所的施工和调试用的工业水、蒸汽等将由需方提接口位置。
(1) The desulfurization and denitrification process follows the principle of mature technology, advanced equipment, stable running, convenient operation and maintenance, high degree of automation, low operating costs and none secondary pollution. High availability, high desulfurization and denitrification rate, low lime consumption, low power consumption and low water consumption are ensured, and the standard of environmental protection is fully met.
(2) The desulfurization and denitrification system takes the boiler type, load, furnace rear desulfurization and denitrification sites, and many other factors into consideration, putting forward a reasonable desulfurization and denitrification process program.
(3) The desulfurization and denitrification process fully considers the characteristics of the boiler. The system resistance is stable. The desulfurization and denitrification device doesn’t affect the normal operating of the boiler in the start, stop, operating and accident handling conditions.
(4) The desulfurization and denitrification process adapts to air quantity, temperature, concentration of SO2 or NOx and other load changes and fluctuations of the boiler.
(5) The deploy of desulfurization & denitrification processes and devices is reasonable, meeting the requirements of placement of eneral layout proposed by the owner. The system and layout described in this paper are the basic requirements by detailed process design, all the engineering demands are achieved to construct a complete desulfurization and denitrification device.
(6) Material conveying and circulation of absorbent of desulfurization and denitrification and the by-products are smooth, with capability matching.
(7) The service life of the main equipment for desulfurization and denitrification is designed to be no less than 15 years.
(8) The absorbent of desulfurization and denitrification is relatively inexpensive and easy to be obtained.
(9) The desulfurization and denitrification device adopts DCS control, and takes the signal connection with the main project into consideration, reserving communication interface.
(10) Water content of desulfurization and denitrification by-product gypsum is less than 10%, and automobile is used for outward transport and comprehensive utilization of the by-product.
(11) The flue gas after desulfurization and denitrification is collected for discharge through chimney (anticorrosion is required and the demander is in charge).
(12) The deploy of all the buildings (structures) in the entire flue gas desulfurization and denitrification system should coordinate with the main project. The deploy should be optimized in the given area according to its engineering design and deploy requirements, so that the process flow and deploy are reasonable, safe and economic.
(13) For the use of water, electricity and gas in the area of desulfurization and denitrification, metering mechanism will be installed on the sub pipeline connected to the total pipeline of the main plant, and the energy metering data is incorporated in the control system for display, reserving the information interface jointing the CEMS system of the main device.
(14)The supplier puts forward requirements on water quality, water pressure and water volume of the industrial water (process water, cooling water of the rotating equipment) required by the flue gas desulfurization and denitrification system, as well as the requirements on the consumption of compressed air for instrument and related parameters. The demander will be responsible for the industrial water source used in the flue gas desulfurization and denitrification system. The demander is also responsible for the compressed air source used by the flue gas desulfurization and denitrification system. Before handing over of the flue gas desulfurization and denitrification system, the industrial water and steam used in construction and commissioning will be provided by the demander.
the industrial water (process water, cooling water of the rotating equipment) required by the flue gas desulfurization and denitrification system, as well as the requirements on the consumption of compressed air for instrument and related parameters. The demander will be responsible for the industrial water source used in the flue gas desulfurization and denitrification system. The demander is also responsible for the compressed air source used by the flue gas desulfurization and denitrification system. Before handing over of the flue gas desulfurization and denitrification system, the industrial water and steam used in construction and commissioning will be provided by the demander.
(四)性能参数及运行分析 / Performance parameters and operation analysis
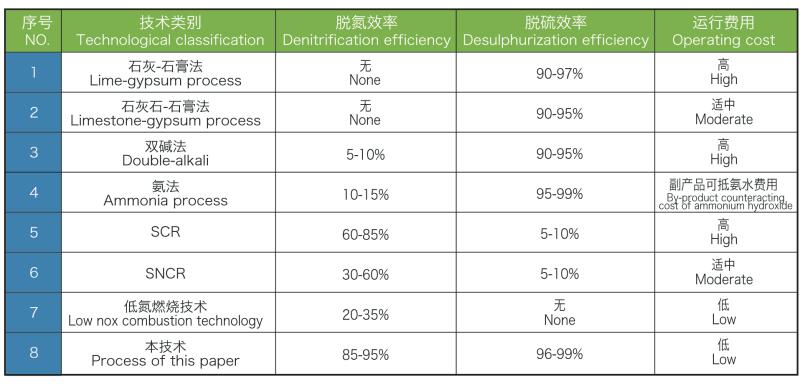